It has been quite a while since 1989, when professional disk mastering system manufacturing came to an end. To be precise, it has been 33 years, during which the world went through a phase of believing that the vinyl record has been rendered obsolete by digital media, followed by a major resurgence over the past decade. Vinyl record manufacturing equipment is large and heavy. It takes up a lot of space, which could be utilized to manufacture something else, such as CDs, bug zappers or toilet paper. During times of low interest in the vinyl record, there wasn’t much of a market for the obsolete manufacturing equipment, except for the one option that is always open for heavy items made of metal: the scrapyard! Record presses, disk mastering lathes and other equipment were melted into soda cans, sewer lids, or worse.
As we discovered during the course of several previous episodes, this had always been a very limited market in the first place and not that many of these machines were ever made. The fact that many of them had been scrapped, and many others had been neglected (left out in the open with no protection from the elements, or stored in damp warehouses, to be frequently bumped by forklift truck operators still suffering the effects of their weekend hangover) meant that by the time the resurgence came and these obsolete chunks of metal suddenly went from being worth their weight in scrap minus the transportation cost to the scrapyard, to being worth insane amounts of money (with prices regularly being readjusted for scarcity with every forklift accident), there really weren’t that many of them left.
A rather young and enthusiastic individual from Switzerland took it upon himself to keep vinyl spinning and to continue the Neumann tradition. Flo Kaufmann, a rather eccentric artist who is notoriously difficult to contact (although this greatly depends on cultural perspective regarding what is considered easy to contact; this statement is made from an American standpoint…) and whose website home page simply states, “welcome to my world of m.e.a.t.” (which stands for Media, Engineering, Art, Technology), had persistently pursued a friendship with the former Neumann employee who had been tasked with fulfilling the contractual obligations for support for Neumann lathes. This contact eventually led to Flo being able to obtain his first Neumann lathe. Apart from cutting records, he went on to offer repairs and servicing of disk mastering lathes, and eventually, along with a group of friends, he started up the FloKaSon company, an entire pressing plant, and developed a range of disk mastering products. One of his first products was the Vinylium Kingston Dubcutter, a portable contraption that could be placed over a Technics SL1200 turntable and could actually cut records. As with other products that were intended for use with the Technics SL1200, its weakest point was the lack of a platter, bearing and drive system designed to withstand the cutting forces.
While the Dubcutter did not go very far as a commercial product, it did come with a stereophonic cutter head (the Vinylium SC-99) that was capable of outstanding results. Many of these cutter heads have since been removed from the original portable unit and used with one of the larger professional disk mastering systems described in the previous episodes.

A Vinylium SC-99 cutter head on a Neumann VMS-70 disk mastering lathe. All images courtesy of Flo Kauffman, FloKaSon.
Sometime after that, another cutter head was to follow, called the Caruso. Very few were made and if used with a good lathe and cutting amplifier system, they are capable of results that can directly compete with any other professional cutter head ever made. I have personally used a Caruso for several years, with a cutting amplifier system of my own design, to much critical acclaim for the results.

FloKaSon Caruso cutter head, on a vintage Thorens lathe overhead mechanism with a Technics turntable.
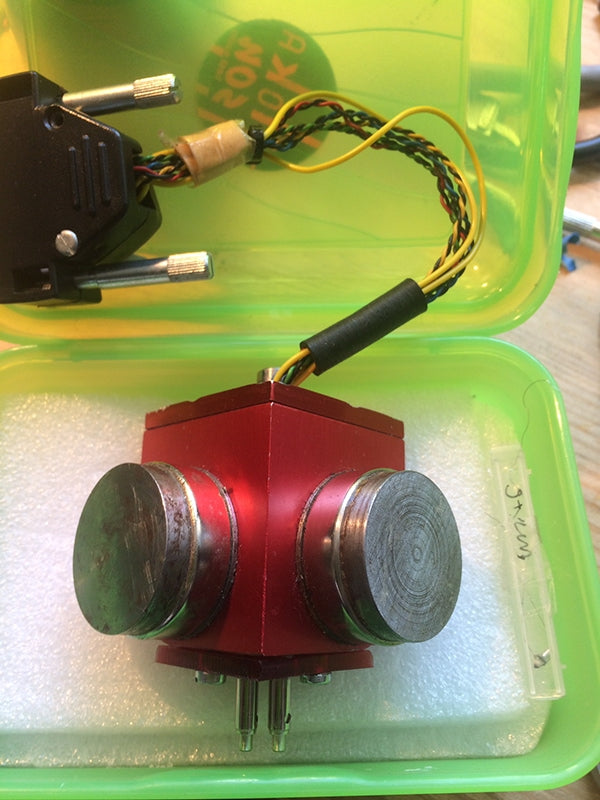
Vinylium SC-99 cutter head.
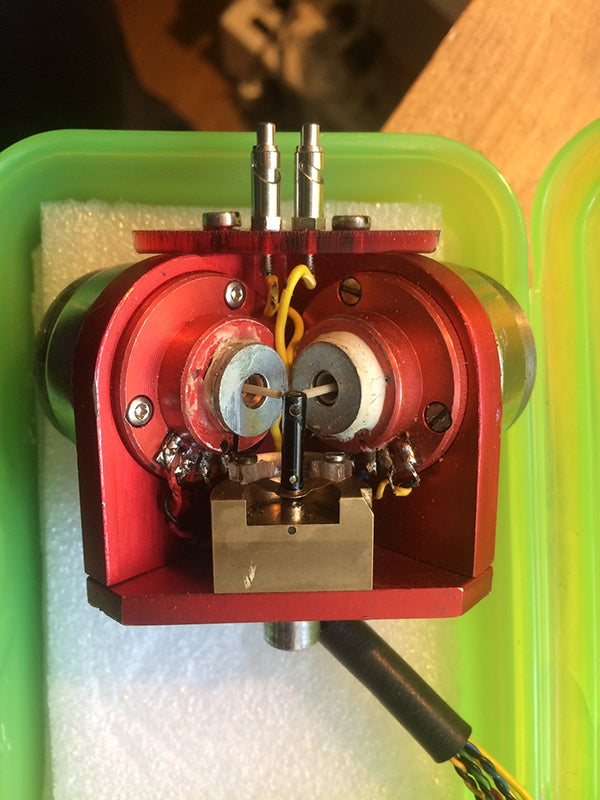
The underside of a Vinylium SC-99 cutter head.
Cutting amplifiers and a pitch/groove depth automation system were also among Kaufmann’s product line. The pitch depth automation systems were introduced in 1998 with the Pitch98, later updated to the Pitch13 in 2013 and the current Pitch18, available since 2018. These systems are perhaps one of the most successful products, developed by Flo Kaufmann and his associate Jvo Studer. They can be found as aftermarket upgrades on several Neumann, Scully, Fairchild and other lathes.
At some point in the 2010s, Flo Kaufmann started the FloKaSon AM44 project, aiming to produce a very limited number of complete disk recording lathes, based on original Neumann lathe beds that had been cast during the World War II materials shortages. Instead of cast aluminum, which is what had been used for all other Neumann beds, these were made of cast iron. They were discovered stashed away in a warehouse in Germany and had never been used to build up a complete lathe. There were around 30 lathe beds, in an as-cast, unmachined condition. There were no other parts, so all other parts had to be made from scratch. I received and put together the first functional prototype to leave the FloKaSon laboratory. Many years of research and development were to follow and by now, a few of these machines can be seen in use around the world.
More recently, Flo has introduced a few additional cutter head models. The DiAlba and LaCallas are a further evolution of the Neumann SX-74, with a focus on added reliability (cutter heads are all generally quite fragile and perhaps the most frequently repaired component of a disk mastering system). Last time I checked, a LaCallas would set you back CHF 33,000, without considering the lathe and cutting electronics needed.
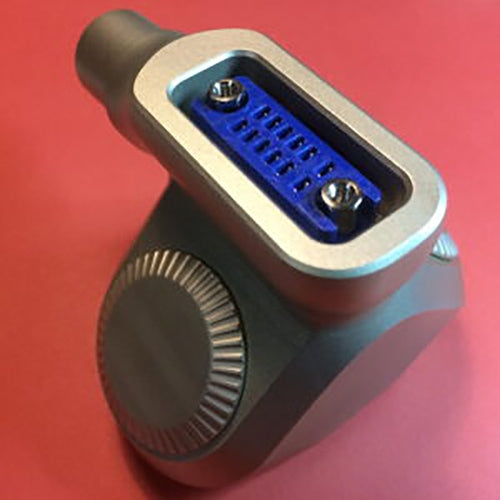
FloKaSon DiAlba cutter head.
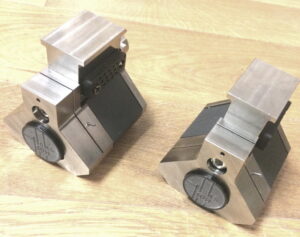
DMM cutter heads made by FloKaSon, along the lines of the Neumann 9X84.

The underside of a FloKaSon LaCallas cutter head.
Following the February 2020 fire at the Apollo Masters Corporation vinyl mastering plant in Banning, California, which destroyed one of the two remaining plants that were manufacturing lacquer disks in the world (the other one being in Japan and still the world’s only remining source for master disks in the world), FloKaSon also made a limited number of SX-84/DMM cutter head copies, to be used on copper disks and offer an alternative for those who would prefer to not rely on lacquer availability.
Flo Kaufmann is also one of the key people behind the Phonocut, a crowd-funded project aiming to develop a fully automated, desktop record cutting machine that can cut on 10-inch blanks. A prototype was presented, but the website informs us that the very earliest the final product could possibly ship is the end of 2024, with a new estimated RRP of €8,000-10,000 (from the originally stated campaign price of €999, later amended to €1,799). The other people and organizations behind the Phonocut are Florian “Doc” Kapps, Creaholic, KamranV, and David Bohnett.
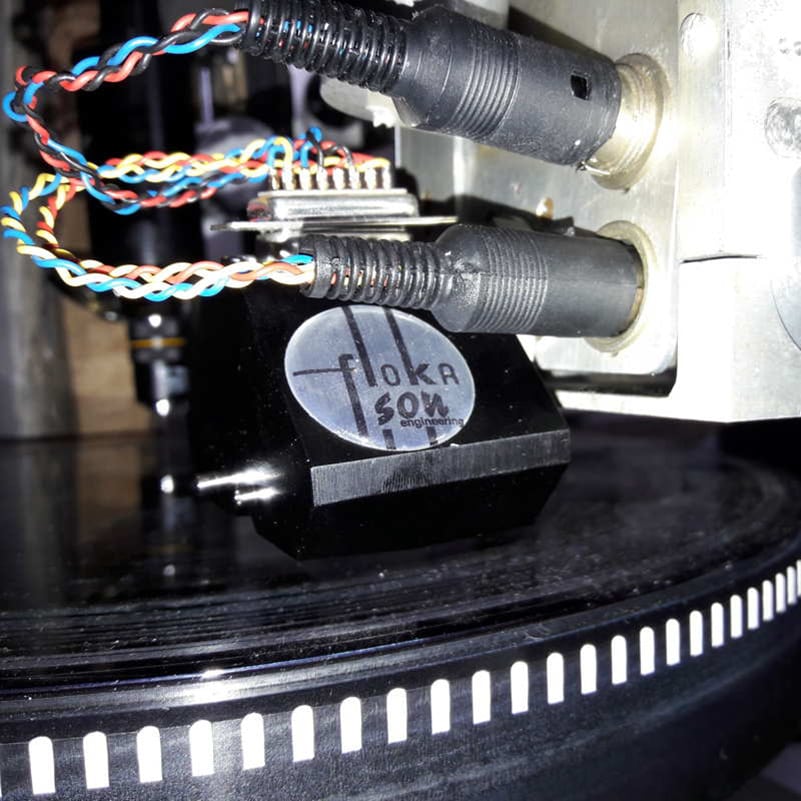
FloKaSon Caruso cutter head.

Inside a FloKaSon brushless DC motor.
Flo is one of only a handful of people (approximately 7 or 8) in the world who is actively working on keeping this technology going and take it a step further where possible. He has been very influential in my own development in this direction, and I have enjoyed conversations and exchanges of information and knowledge with him over the years. As with several other people involved in this sector, his other interests include large-format photography (on film), classic cars, and homemade electronic musical instruments. His main artistic occupation involves art installations using electronics and audio and video technology under the project name bricolage universel. One of his performances involved cutting a record groove on a beer can.

FloKaSon cutting electronics.
Header image: a Neumann-based FloKaSon AM44 disk mastering lathe. Courtesy of Flo Kaufmann.
Previous installments appeared in Issues 165, 164, 163, 162, 161, 160, 159, 158, 157, 156, 155, 154, 153, 152, and 151.