Over the last several episodes, we have traveled to different parts of the world to look at the different engineering cultures in different times and places, all sharing a common goal: the recording of music on round disks in the form of modulated grooves. The approaches have been quite different, even wildly so at times, and the different record cutting lathes all had strengths and weaknesses.
The beauty of disk recording and mastering lathes lies in the inherent simplicity and modularity of the technology. On the playback side of things, it was (and still remains) common to purchase a turntable, fit a tonearm made by a different company and then try out a few different cartridges, made by other manufacturers, before settling on the combination that appears to sound best on that particular system. Then comes the phono stage, either standalone or part of a preamplifier that has one built in. This will take the small signal coming out of the cartridge, apply the RIAA de-emphasis, amplify it into a line level signal and drive a power amplifier with it. The phono stage or preamp and the power amp could of course be made by separate manufacturers, none of which have anything to do with the turntable, tonearm or cartridge used. Then we have loudspeakers, crossovers, speaker cables, room acoustics… Each one of these items is worth writing a rather thick book about.
However, without needing to necessarily know how to design such components from first principles, the seasoned audiophile will be very familiar with what each of these components do in a system. They can mix and match until they are satisfied with the result, or just keep on trying out different combinations eternally, convinced that the real reward is the journey and not any particular destination.
Similarly, the components of a disk mastering system can be mixed and matched ad perpetuum and it was just as common to do so for many decades, up until Neumann made it their main selling point to provide a complete system, so you wouldn’t need to worry about figuring out how to mix and match the various components. Admittedly, this kind of mixing and matching of lathe parts is significantly more complicated than the equivalent on the reproducing side, with far fewer products to choose from, a far lesser degree of standardization (read as, “nothing will just bolt right on”) and no magazines explaining in simple terms how to adjust things.
Still, all a disk recording system is, essentially, is a platter rotating at the right speed with a means to clamp a disk on it, a mechanism that advances a cutter head across the disk surface, and a cutter head capable of wiggling a cutting stylus to modulate the groove. The first two form the transport and the last part constitutes the audio portion of the system. The lathe bed would, in very broad terms, keep the platter spindle and the carriage slide system at 90 degrees to each other without transmitting vibrations from one to the other. All Neumann lathes, all Scully lathes, all Western Electric lathes and a couple of Presto models (the 8D/8DG and the 14B) featured machine-tool beds, similar in design to the beds found on screw-cutting lathes, but with a vertical spindle instead of a horizontal one needed to make screws. All other disk recording lathes had “beds” that were more like the plinths found on reproducing turntables, where everything was bolted. Both approaches could be made to work exceptionally well, but the machine tool bed approach dominated the disk mastering market.
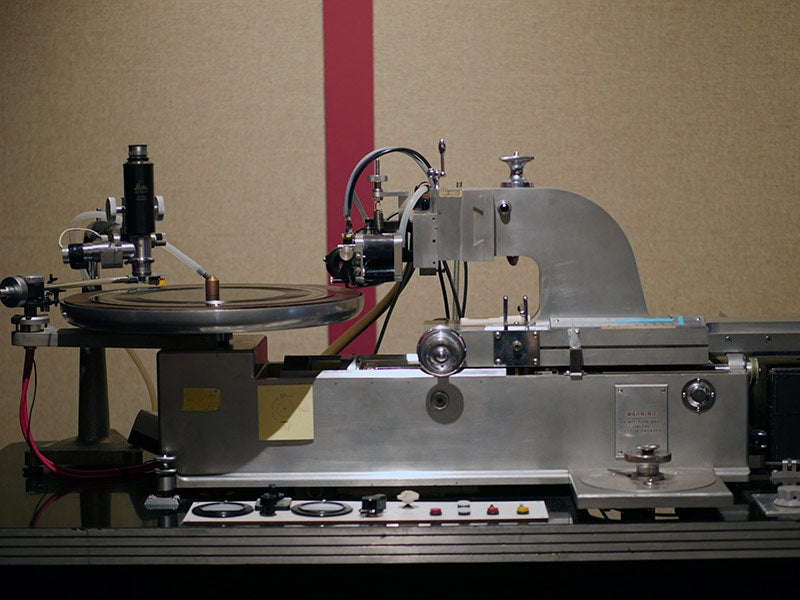
Scully lathe, shown in its original configuration. Courtesy of Artone Studio, Haarlem, The Netherlands.
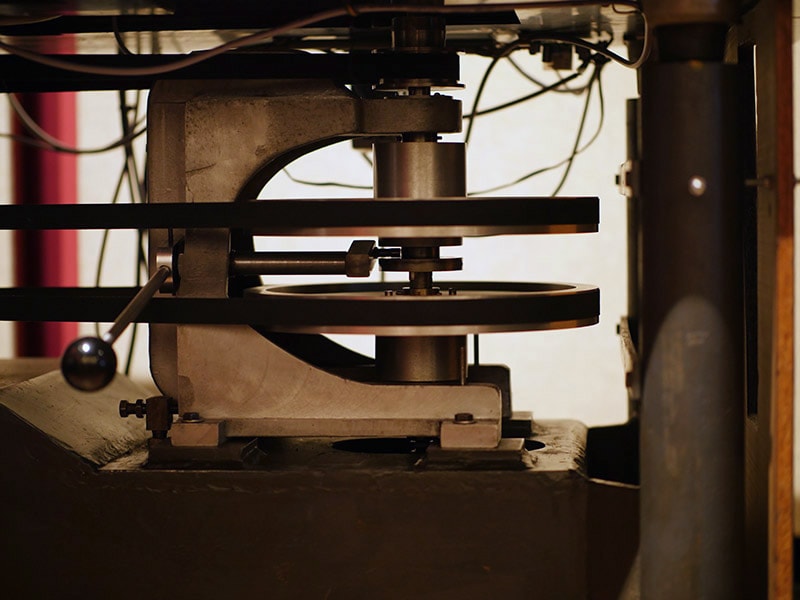
Detailed view of the original Scully belt-drive system. Courtesy of Artone Studio.
By the end of the 1960s, there were very few other lathes to be seen in a mastering studio, besides Neumann and Scully models. But this primarily refers to the lathe bed, as everything else could be mixed and matched, so a Scully lathe did not necessarily need to have much more than just the Scully bed, with parts made by other manufacturers bolted to it. Despite the best efforts of Neumann, their products were also frequently modified. By now, with no OEM support or replacement parts to be found, most disk recording and mastering lathes in active service are built like hot rods, using the highest-performance components that can be found to squeeze the last drop of fidelity out of the system.
Most lathes had main bearing units that bolted onto the bed, so these too could be replaced, as could the spindles and the platters. David Manley built up a mastering system consisting of a Scully lathe bed with a Neumann vacuum platter, and several other Scully lathes are wearing Agnew Analog vacuum platters now. Most Scully lathes were originally belt-driven, but some were modified to be driven by a Lyrec SM-8 direct-drive motor, while others were modified to be driven by Technics SP-10 turntables on the floor under the lathe (Bernie Grundman is using this configuration). David Manley was using a Technics SP-02, and a few are using the Agnew Analog Type 631 direct drive motor. Floorstanding direct-drive motors and turntables of course needed a custom driveshaft to transmit motion to the platter.

An extensively modified one-off Scully lathe, fitted with a Neumann vacuum platter, driven by a Technics SP-02 motor, with a Westrex cutter head driven by Manley Laboratories tube amplifiers. It was put together by David Manley. Courtesy of Manley Labs. Note: Manley does not currently build or modify lathe systems.
The mechanical assembly of the carriage usually relied on a separate motor to drive, or on a power take-off from the main drive system for the platter. This could be endlessly modified, replacing the motors and the control electronics to create all sorts of automation systems. Even though Neumann lathes had some of the most sophisticated control electronics and automation systems of the time, fitted from the factory, the majority of them have by now been replaced by aftermarket pitch control systems, with several options available. Many Scully, Presto and Fairchild lathes did not come with any automation, but many of these have been retrofitted with modern control electronics.
Suspension units for the cutter head came in many flavors. Floating cutter heads had different particularities to those equipped with an advance ball (which would ride ahead of the cutting system to control the depth of cut; see my article in Issue 162), so the suspension units were usually designed to better suit one of the two methods of holding a cutter head. The more advanced suspension units had electronic depth control systems (for floating heads), electronic head drop/lift systems, and various other bells and whistles. On Neumann and Scully lathes, the suspension unit was attached to the end of the carriage arm, and it was a very simple procedure to remove it and replace it. On other lathes, the suspension unit was integral to the carriage, making it more complicated to entirely replace it, but possible to modify as needed.
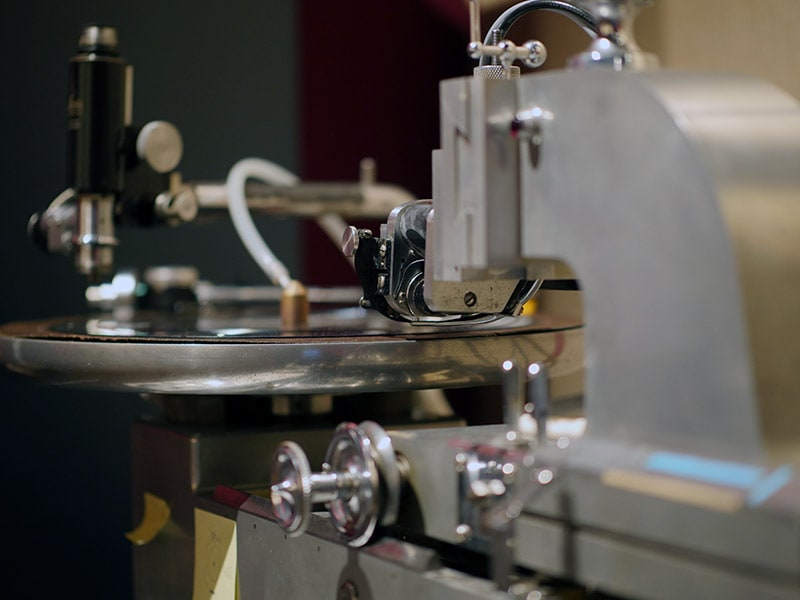
The Scully lathe carriage. Photo courtesy of Artone Studio.
The cutter head itself was almost as easy to replace as the cartridge on a tonearm, with the difference that there was no standardized mount that was common to all lathes. By the 1950s, each lathe manufacturer was using their own proprietary (and entirely incompatible with anything else) cutter head mounting system. Fortunately, adapters could be easily made, making it possible to fit pretty much any cutter head to almost any lathe out there. By far the largest and heaviest cutter heads were those made by Westrex. Scully lathes were designed to carry these, so they could handle any cutter head you wanted to use, with no issues. A Neumann stereo head was about four times lighter than a Westrex stereo head, but around four times heavier than an RCA mono head. A Neumann lathe could easily take any lightweight mono head but needed some modifications to handle a Westrex head. A Scully or HAECO suspension unit could, however, be fitted to a Neumann lathe. The HAECO suspension unit was a popular aftermarket option for Scully lathes. Scully lathes have been equipped with all kinds of suspension units and cutter heads. Most often seen with the Westrex cutter heads, they were frequently also fitted with Ortofon and even Neumann cutter heads, sometimes with the Neumann suspension unit as well.

Scully lathe with Westrex 2B cutter head. Courtesy of Artone Studio.
The LP artwork of Lincoln Mayorga and Distinguished Colleagues, Volumes I, II, and III all feature photographs of Scully lathes with Neumann cutter heads held on a rather intense-looking custom suspension unit. By 1978, the artwork of the Sheffield Lab direct-to-disk recordings of Wagner’s works, performed by the Los Angeles Philharmonic and conducted by Erich Leinsdorf, show several Neumann lathes, with modifications.
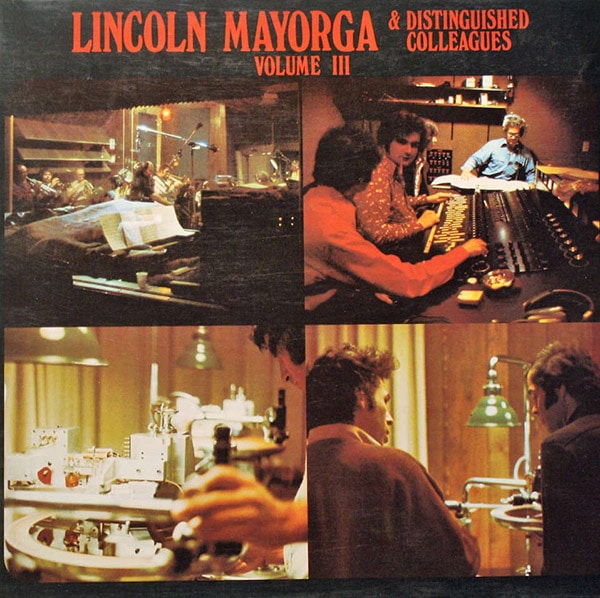
Lincoln Mayorga and Distinguished Colleagues, Volume III, album cover.
Unlike driving loudspeakers with power amplifiers, the cutting amplifier rack intended for driving a cutter head was a little bit more complicated. Not only was each cutting amplifier specifically designed for a particular cutter head, but even then, two seemingly identical cutter heads of the same make and model were not interchangeable on the same cutting amplifier rack. This was due to the use of motional feedback, using signals generated by dedicated feedback coils within the cutter head to correct errors and linearize the system, as well as sophisticated instrumentation for cutter head protection, current metering, and remote temperature sensing, accomplished by means of a resistance bridge (sensing variations in the DC resistance of the drive coils due to temperature, without affecting the AC audio signals driving these coils).
At best, with two identical cutter heads, the electronics would need to be recalibrated when switching from one head to the other. Alternatively, circuit boards could be swapped along with the head, having a set of pre-calibrated boards matched to each channel of each head.
When entirely different cutter heads had to be used, significant modifications were often required to “convince” a cutting amplifier designed for a particular model of cutter head to work with another. Not only was this done, however, it was not uncommon for mastering facilities to modify and upgrade their cutting amplifiers, building their own from scratch, or using high-end amplifiers intended for loudspeakers, with additional circuitry, to drive cutter heads.
A certain culture of fiddling and hot-rodding has always surrounded disk recording systems. It was perhaps due to this culture that the advances in sound quality kept on happening over so many decades. It keeps things exciting and sustains the notion that great rewards come with great effort, which has kept the disk medium alive and well since Emile Berliner’s early experiments. There are certainly simpler ways to record and reproduce music. But are they as rewarding?
Header image: a heavily-modified Scully lathe, at Organic Music, Obing, Germany. It has been converted to direct-drive with a floated Vinylium SC99 cutter head, driven by amplifiers! Courtesy of Thorsten Scheffner, Organic Music.