Phonograph disc reproduction cartridges (phono cartridges as they’re known to you and me) all contain transducers consisting of coils of wire, iron and permanent magnets. They can be divided into three main categories: moving magnet, moving iron, or moving coil, based on their principle of operation.
What differs is the actual configuration of the elements they’re made from. All do the same thing: translate the motion of the stylus and cantilever (the shaft the stylus is mounted on) into electrical impulses that correspond to the information contained in the record groove.
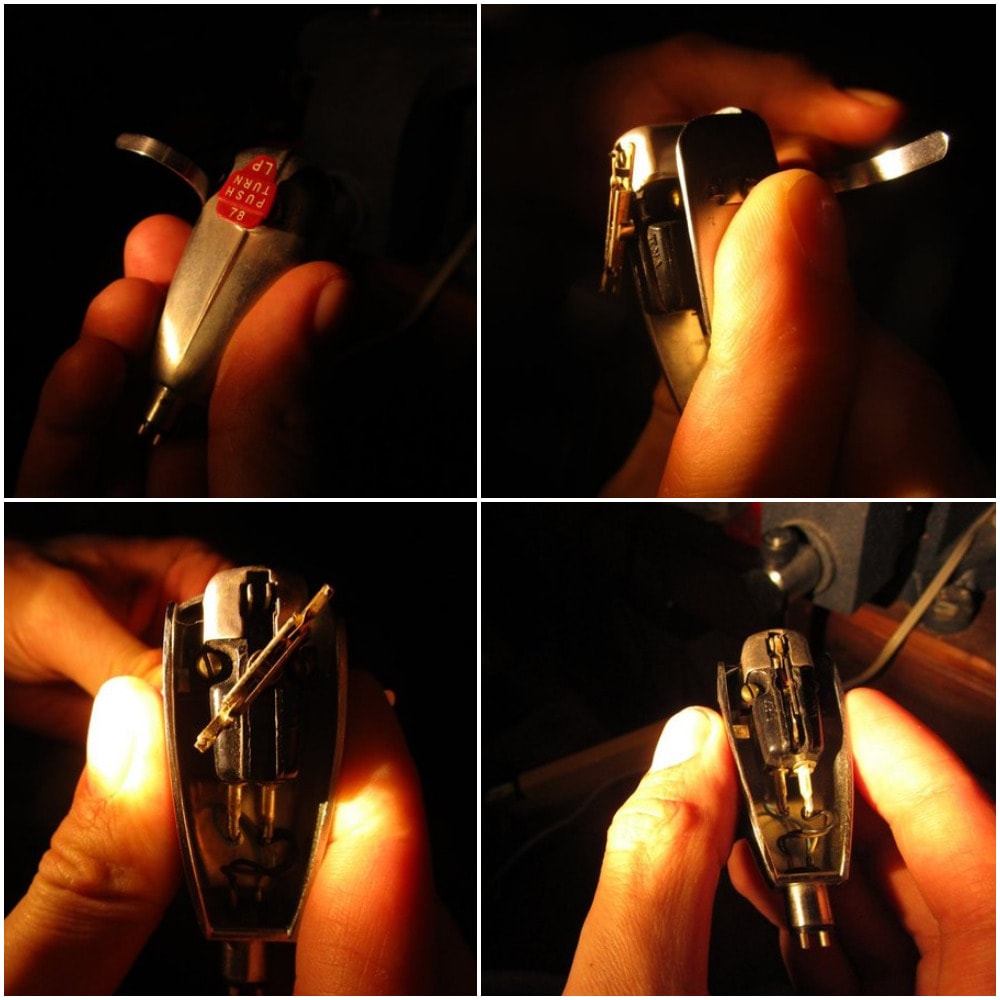
General Electric VR-II: this is a vintage monophonic moving iron cartridge, featuring two styli, one with a large tip radius for 78 RPM records and one with a small tip radius for 33-1/3 RPM "microgroove" records.
Starting from the record surface upwards: all phono cartridges have a stylus (usually made of diamond nowadays) which rides in the groove. This stylus is shaped in forms as simple as a cone (spherical tip), or as complex as the multiple variations on the line-contact theme (elliptical, Shibata and others). Simply put, the spherical tip’s foremost advantage is low cost. Its main disadvantages are its inability to trace sharp curves due to high levels of groove modulation at high frequencies, and its inability to follow the exact same path inscribed by the cutting stylus when the record was cut, due to its shape significantly deviating from the shape of the cutting stylus. Both of these phenomena result in tracing distortion upon playback.

Van den Hul MC Two moving coil cartridge on an SME tonearm. This cartridge features a line-contact stylus on a boron cantilever.
However, if the playback stylus were to be shaped like a cutting stylus, it would actually cut into the grooves and ruin our records. So, the trick is to find ways to geometrically approximate the shape of the cutting stylus, while removing any features that would actually be able to cut and do damage.
The result is the different approaches to line-contact styli. Not only do line-contact designs follow the same path as the cutting stylus to a much greater extent, they are also able to trace at higher levels at higher frequencies and shorter wavelengths, thus reducing the various forms of tracing distortion, including inner groove distortion. The latter occurs due to the reducing linear velocity of the groove at smaller diameters, resulting in smaller recorded wavelengths and therefore sharper curves as the record groove gets closer to the end of the disk.
As an added bonus, although they contact a thinner section of the groove, the more elaborate line-contact designs increase the
depth of contact and as such, the total contact area between the groove wall and the stylus. This has two beneficial, if somewhat not-obvious effects: One, distributing the vertical tracking force over a larger area results in lower pressure on the record surface, reducing record wear and distortion due to elastic (and sometimes even plastic) deformation of the groove under the pressure of the stylus.
Two, it also reduces the noise floor by more effectively “averaging” the individual PVC molecules that make up the groove wall, which define the ultimate noise floor of the medium. Averaging reduces the statistical probability that a single discrete PVC molecule would be traced to translate into sound, thereby reducing the noise level. This same mechanism has formed the basis of many publications concerned with surface metrology (the measurement of small-scale features on surfaces), a subject of continuing research at national laboratories and standards institutes.
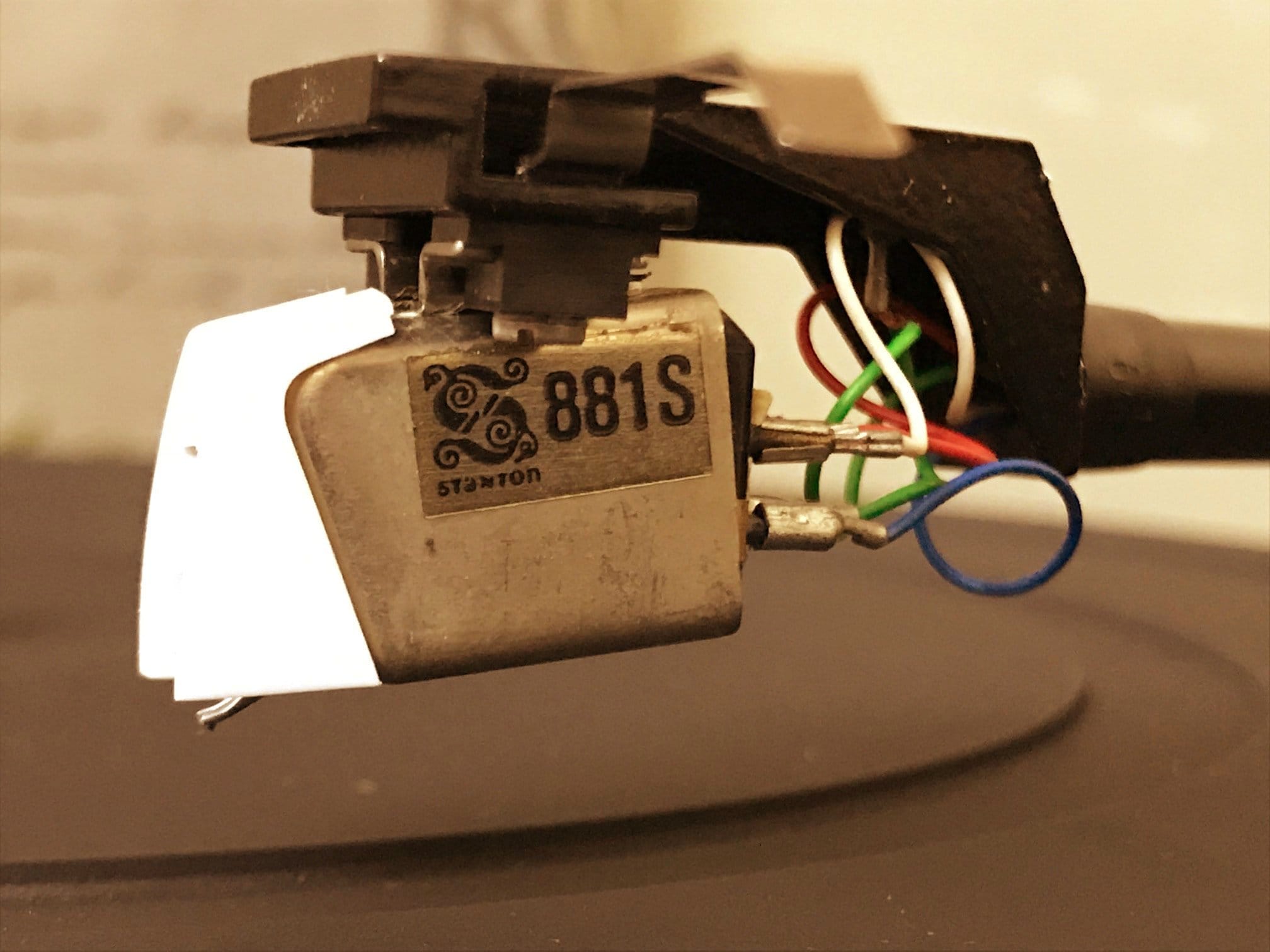
Stanton 881S Reference Series moving magnet cartridge with stereohedron stylus.
The downside is that line-contact styli are considerably more difficult to manufacture and require precise orientation upon installation, which is why they cost more.
The stylus is installed on the cantilever, a miniature beam which must accurately transmit the stylus motion to the transducer elements. This is often made of aluminum, boron, or more exotic materials. It must combine extremely low mass (to not impede the incredible accelerations encountered on record grooves) with extremely high rigidity (to not bend instead of transmitting the motion where it ought to). Any bending or vibrational modes in the cantilever would cause it to deviate from the required accuracy of reproduction.
The cantilever is suspended, usually by means of an elastomer and/or wire spring, so it can move freely as required, while returning to its neutral position in the absence of sound and without any tendency to continue moving, pendulum-style, after the impulse setting it into motion is removed.
The other end of the cantilever carries the moving element of the transducer system. This can be a magnet, iron, or coil, as the category names would imply. In any case, this element also contributes to the transducer’s moving mass, which must be kept astonishingly low to achieve a proper high frequency response.
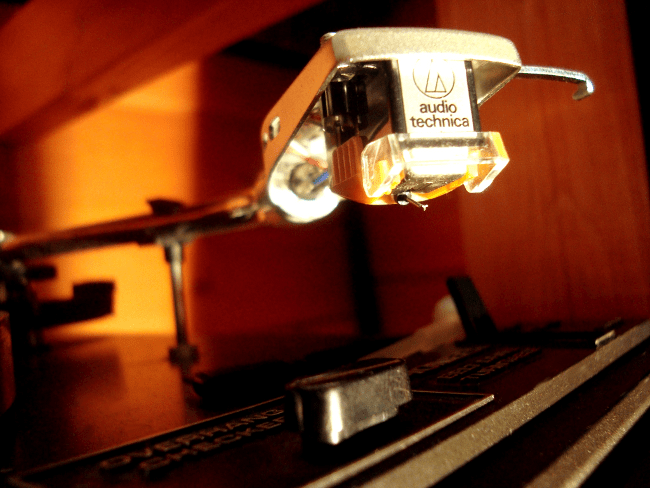
Audio-Technica AR12XE moving magnet cartridge with line-contact stylus.
This assembly is mounted close to the rest of the transducer elements, which remain stationary. The transducer and moving parts are all attached to the cartridge body, which also contains some provision for mounting to a tonearm headshell.
While the stationary elements of the transducer and the rest of the cartridge body do not contribute to the moving mass of the cartridge and therefore have no mechanical effect on the high frequency response, the total mass of the cartridge adds to the effective mass of the tonearm. This, along with the cantilever suspension compliance – the stiffness of the stylus cantilever (with high compliance being softer and low compliance being stiffer) – defines the low frequency response of the cartridge/tonearm system by shaping the mass/compliance resonance at a (hopefully) subsonic frequency, below which the low frequency response sharply drops off.
The effective mass of the tonearm and the compliance of the cantilever determine the
resonant frequency of the arm/cartridge combination. This is the frequency at which the cantilever will literally resonate or vibrate out of control. As a result, it’s necessary to carefully match the effective mass and the compliance so that the resonant frequency isn’t in a range where it will be excited by record warps or intentional groove modulation (sound).
Not only does this resonance define the frequency response of the arm/cartridge at the low frequencies, but it also defines the phase response, which extends higher than the cut-off frequency itself. An incorrectly tuned system will ruin the phase accuracy well into the audible portion of the spectrum and will either kill the bass or boost it to the point where the stylus will no longer stay in the groove!
Carefully pairing the tonearm with a compatible cartridge serves to tune this resonant frequency, placing it where it should be, usually around 10 Hz.
The response and performance of a system are also affected by electrical and geometric factors.
The electrical factors get more complicated and include eddy-current losses, wiring capacitance, coil inductance and other considerations. Eddy current losses, caused in a conductive material by a changing magnetic field, occur in the transducer components and reduce the high frequency response. They can be controlled through careful design of the transducer. Inductance and capacitance form a resonant circuit, which affects the frequency and phase response. An inductance/capacitance resonance causing a rising response at the high frequencies could be balanced out by eddy current losses through careful design, but the whole system can be thrown off balance if the total system capacitance (including the wiring and preamp) is not set according to the value given by the cartridge manufacturer. (This parameter is adjustable in many phono stages and preamps.)
The arm/cartridge system is designed for a certain value of vertical tracking force (VTF), which is adjustable on the tonearm to suit a range of different cartridges. Incorrect VTF setting will result in distortion and response errors.
A frequently misunderstood parameter is vertical tracking angle (VTA). This is not the angle formed by the stylus leaning forwards or backwards rather than being at exactly at 90 degree to the record surface; that would be the stylus rake angle (SRA). The VTA is the angle of the vertical plane of modulation that is cut on the record. This must be exactly matched by the cartridge’s vertical plane of tracking for accurate reproduction.
The VTA is a dynamic parameter, not a static one. This means that it cannot be accurately measured statically, as a simple geometric feature of the cartridge. This parameter is affected by the dynamics of the revolving record, the moving tonearm and the vibrating stylus. Its calculation is not exactly straightforward and is usually accomplished by means of a special test record and laboratory measurement instruments. VTA and SRA are both geometric factors.
The reproducing stylus rake angle must also match the cutting stylus rake angle for accurate record playback.
However, since the reproducing stylus (of the cartridge) is permanently attached on the cantilever at a certain orientation, the cantilever is also suspended at a certain orientation and the transducer registers at a certain angle in the vertical plane, the relationship between SRA and VTA is fixed by the manufacturer for each cartridge and cannot be altered by the user. As such, changing one of these parameters also changes the other. In practice, these parameters were not intended to be user-adjustable, although there is plenty of discussion on tweaking them all over the internet. Since both of these parameters must match both equivalent parameters as these were set cutting the records, it would be vital for the cartridge manufacturers to have a solid understanding (if not first-hand experience) of how records are cut, so the correct values of VTA and SRA can be designed into the cartridge.
So, what are the correct values of VTA and SRA? The answer is...I wish there was a simple, single, correct answer.
In fact, the relationship of these two parameters was a bit different on each model of cutter head used to cut records. The exact value also depends on which lathe the cutter head would be fitted to, and how it would be set up. Especially VTA, being a dynamic value, is rather complicated to accurately measure. This is a big part of the reason why different cartridges of a similar level of quality, transducer type, stylus shape and materials, can sound so different to each other when playing back the same record.
The VTA and SRA values of one cartridge may happen to more closely match the values of the equivalent parameters when the record was cut, so that cartridge sounds better because it
is actually better matched for reproducing that particular record. Change to a different record and another cartridge might sound better. There are, sadly, also cartridges designed with little regard to how records are actually cut, and these cartridges simply would never stand a chance of accurately reproducing a record, regardless of the amount of unicorn hair used to manufacture them under the full moon on a particular night of the year.
It is not just about the materials or the type of transducer used in cartridge manufacturing. A cartridge needs to be designed to reproduce real-life records, as they were actually cut.
If the geometric parameters are sensibly designed into a cartridge, along with the use of high-quality materials, a stylus shape that accurately traces the record groove and an accurate transducer system, one can be assured that such a cartridge will be a worthwhile investment.