For some reason, the people involved with the manufacturing of vinyl records are rather stoic types. The rare occasion when they are in a talkative mood, they mostly talk about the manufacturing process and equipment. They are not often talking about what happens after the records have been manufactured, the actual reproduction of these records, for pleasure or for the most critical step of manufacturing: quality control.
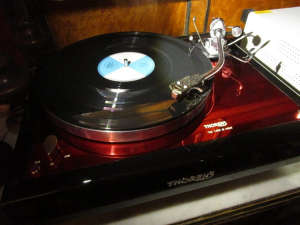
What follows is the story of the restoration, modification, assembly, calibration and testing, of some components, which, if used properly, can result in a highly accurate phonograph disk reproduction system.
This system is now being used along with a few other systems offering similarly accurate performance, as a reference for the evaluation of vinyl record manufacturing equipment and in particular, disk mastering systems and the resulting records they produce.
Being involved in the design, development, testing, manufacturing, and repair of disk mastering equipment and also cutting masters for vinyl record manufacturing, we need some reliable reproduction systems for our measurements, listening tests and even listening pleasure.
The Thorens TD 160 is a highly regarded, classic turntable, which was manufactured in Lahr, Germany, from 1972 to 1988. In 1976 the TD 160 Mk II was introduced and the TD 160 Super arrived in 1982. All variants are simple and well-designed, offering a very high level of performance straight out of the box. All versions come fitted with the Thorens TP16 tonearm, in one of its implementations, which is already quite decent, but there is ample room for improvement.
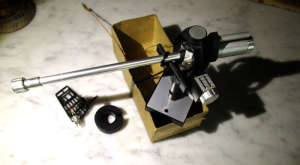
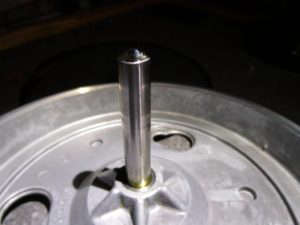
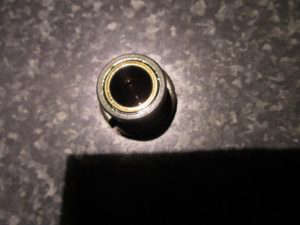
The center bearing is comprised of a couple of plain bronze bearings in a housing, terminating in an accurately machined cone which engages a matching cone at the bottom of the shaft. No ball! Friction and noise are exceptionally low, while accuracy is high, as expected from a Swiss manufacturer (at least this was where they started!) of precision parts.
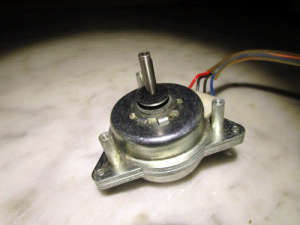
The motor is a 16-pole synchronous AC unit, with a clutch pulley to ensure a smooth start. By now, the original capacitors on these units have developed a rather high leakage current, causing the motor spindle to vibrate as soon as it is plugged in with the switch in the "0" position. Just touch the top of the pulley and you can feel it. This is not normal, and can easily be rectified.
The platter is belt driven and the two-step motor pulley is configured to offer the correct ratio for 33 1/3 and 45 rpm.
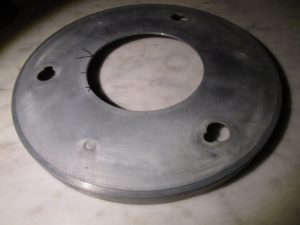
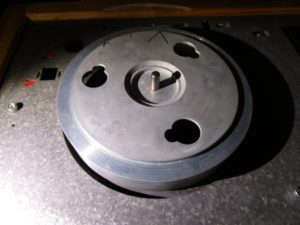
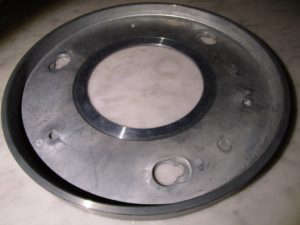
Through the years, we have taken apart and rebuilt, repaired and/or modified all variants of the TD 160. The early version, called simply the TD 160, had the same 10 mm shaft and bearings as the TD 125. It came with the early version of the TP16 tonearm, with the TP60 detachable headshell, same as was fitted to the TD 125 Mk II. All TD 160 variants have the same platter and motor as the Thorens TD 125 and TD 126, including the TD 125 Mk II and TD 126 Mk II.
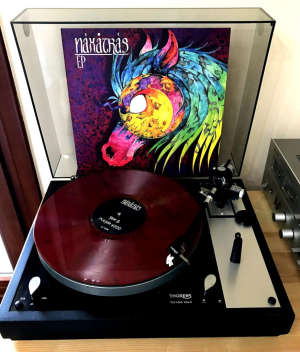
The TD 160 Mk II had a smaller diameter platter shaft, retaining the same cone arrangement. The bearing unit is configured a bit differently and the housing is also slightly different. The motor remains the same but the clutch pulley has some minor improvements. It is fitted with the TP16 Mk II Isotrack tonearm, which features a detachable wand called the TP62, instead of a detachable headshell, thereby reducing the effective mass of the tonearm to just 7.5 g. By comparison, the effective mass of the early TP16 with the TP60 headshell was 16.5 g!
The TD 160 Super came with the TP16 Mk III tonearm, had a different plinth and a damped motor plate.
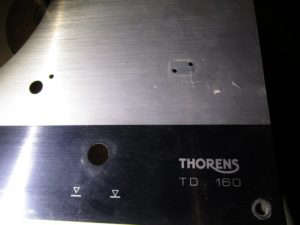
All variants can occasionally be found nowadays hiding in attics and basements in various stages of deterioration, awaiting to be found and lovingly restored.
The tonearm we chose for this project is an SME 3009 Series II Improved, an evolution of the earlier 3009 dating from 1975, with a much more sophisticated decoupling of the counterweight for better resonance control. This tonearm was widely used in professional applications where sound quality was of prime importance. This was a substantial improvement over the TP16. The SME 3009 was introduced in 1959 and was a hugely influential design.
The SME 3009 Series II Improved, with a fixed headshell (superior in performance to the removable headshell version) has an effective mass of only 6.5 g. The maximum vertical tracking force (VTF) it was intended for was 1.75 g.
Looking for a moving coil cartridge that would be a good match for this tonearm was not an easy task. Many manufacturers nowadays are opting for low-compliance designs requiring a VTF of over 2 g. The typical match for this tonearm was the Shure V15 range of moving magnet cartridges. We do use a Shure V15 III on another SME 3009 tonearm on a different turntable, as a reference, so for this system we wanted a moving-coil cartridge of high performance.
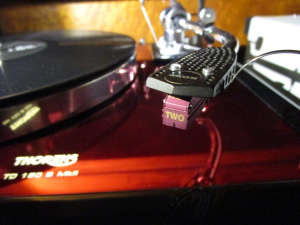
The van den Hul MC-Two specifications made it seem like a potential candidate, so we decided to give it a try and see how it measured. This is a handcrafted moving-coil cartridge, designed and built by Mr Aalt Jouk van den Hul in The Netherlands. It is fitted with a boron cantilever and a nude diamond type VDH-I stylus, 3 x 85 μm, also designed by A. J. van den Hul and bearing his initials (VDH). The van den Hul MC-Two is a higher output version of the van den Hul MC-One. The entire range of van den Hul cartridges are very highly regarded, but the specifications appeared a bit optimistic at first glance. Frequency range 5 Hz – 50 kHz, channel balance <0.5 dB and channel separation >35 dB? Well, we'll see about that when we get to the measurements...
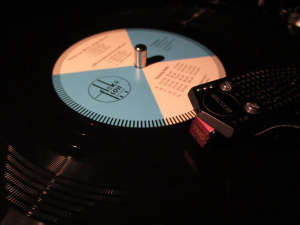
We used the FloKaSon Testtone Record Vol.1, along with a few custom test records cut by J. I. Agnew for our laboratory measurements. With these, we could accurately adjust the cartridge/tonearm combination and measure its performance.
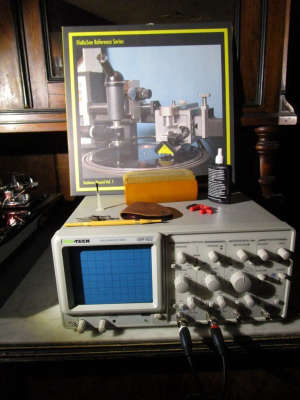
Starting with the lowest value of VTF that the manufacturer recommends, 1.3 g, the channel separation was an appalling 12 dB, so this was promptly increased to 1.5 g. Better, but not quite there yet. This was just a quick observation on the scope while reproducing the first left channel 1 kHz tone. Adjusting tonearm height, overhang, lateral balance, lateral alignment, and then fine-tuning the VTF along with the anti-skating force, while reproducing the different bands to check different aspects of performance, took a few hours of intense concentration.
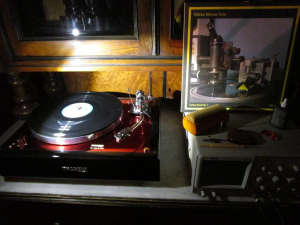
At this stage it would be appropriate to make a point about tonearm height adjustment and how this relates to vertical tracking angle (VTA) and stylus rake angle (SRA) adjustment. Arm height adjustment serves to make the tonearm wand parallel to the record surface with the cartridge down at the final vertical tracking force (VTF) setting, so the dynamic parameters work as designed. The cartridge VTA is 22 degrees and the SRA is 1 degree on this particular model. These are defined by the designer of the cartridge and the relationship between them is fixed. Which means, if we tilt the cartridge forward to increase VTA to 25 degrees, SRA will also increase to 4 degrees.
Considering the length of the tonearm, increasing its height at the pivot will not have a substantial effect on VTA/SRA! To effect a change of even 1 degree in VTA/SRA, the tonearm height would have to change by over 4 mm, which is not a good idea.
If it is required to deviate significantly from the design values of VTA/SRA of a given cartridge, this can only be done correctly by means of a special headshell or mounting adapter.
We have made such mounting adapters, allowing the continuous adjustment of cartridge body tilt for any desired value of VTA/SRA.
So, once the several iterations of adjust, measure, adjust some more, measure even more, were completed, we had the following results:
Frequency Response: 12 Hz-50 kHz +/-1 dB
Tracking Ability: 70 μm
Channel Balance: 0.4 dB
Channel Separation: 28 dB
Output Voltage: 2.3 mVrms
Primary System Resonance: 10.5 Hz
Rumble Weighted (DIN 45539): -78 dB
Wow & Flutter Weighted Peak (DIN 45507): 0.03%
These are quite close to the specifications offered by the manufacturer, apart from the channel separation. However, it should be noted that it is extremely difficult to measure anything over 29 – 30 dB of channel separation on any cartridge using a test record. This is a topic for an entire book on the accuracy of different measurement methods. Specifications stating over 30 dB of channel separation do not necessarily mean that you will ever get to see or hear that in practice when reproducing a record.
The tracking ability was at the lower end of the published specifications, which stated 70 – 80 μm. This is adequate for most practical purposes. Few cartridges tested thus far have actually passed the 100 μm tracking ability band. These include the Shure V15 in different variants, the EMT TSD-15 (freshly reconditioned with new suspension) and an Audio-Technica AT12XE. Most decent ones go up to 70 – 80 μm, but no further. They can still sound great though.
The channel balance was impressively accurate, mostly within 0.2 dB throughout the entire range, with the worst points going down to 0.4 dB, exceeding the published figure of 0.5 dB! This is exemplary performance, very rarely encountered in any kind of real-world transducer. These figures really test the limits of the measurement equipment and the skill of their operator.
As for the frequency response, this is indeed very impressive and confirms the specifications. There is, however, a small catch. Notice how the original specs state 5 Hz while our measurements show 12 Hz? Well, the cartridge alone can probably go down to 5 Hz. However, it is normally fitted to a tonearm. The cartridge cantilever has a certain compliance, given as 28 μm/mN, statically measured. It also has a certain mass. The manufacturer states 8.2 g, but we measured 7.95 g. Add to that the mounting screws, finger lift, headshell, effective tonearm mass, etc, and we are at around 17 g.
The compliant suspension of a mass results in an oscillatory system, fortunately damped to some extent. The resonant frequency of this oscillatory system can be predicted mathematically:
where M = Mass
C = Compliance
To make it more convenient, we could use M directly in g instead of kg and C in μm/mN, by rearranging it as follows:
Where M' = Mass in grams
C' = Compliance in μm/mN
If we were to use the static compliance value of 28 μm/mN, we would get an fres of 7.3 Hz, which would be incorrect. The cartridge is meant to reproduce a spinning record, not a stationary one, so we are interested in the dynamic compliance, not the static compliance. The static value is simpler and faster to measure though, so this is what most manufacturers will offer.
Taking an educated guess, we could assume that a static compliance of 28 μm/mN would translate to a dynamic compliance of half this value, so 14 μm/mN or somewhere around there. This brings us to 10.36 Hz, which is exactly where we would ideally want to be. A tonearm/cartridge resonance of approximately 10 Hz is recommended, which could be stretched to a range from 8 Hz to 12 Hz in most cases, without side effects.
An effect of this resonance is that it results in a mechanical high-pass filter, attenuating below the resonant frequency. This prevents the tonearm/cartridge combination from achieving a flat response down to 5 Hz.
But, what if we add more mass? Yes, we could do that and get a response flat to 5 Hz, by lowering the resonant frequency. Unfortunately, records are not perfectly flat, so if we were to do that we would get a lot of strange audible side effects which are magically tuned out once the resonance frequency reaches or exceeds 8 Hz. Exceeding 12 Hz, on the other hand, unnecessarily interferes with the phase response and increases the risk of the needle jumping if the resonance is excited by recorded sounds. As an example, the lowest fundamental of a pipe organ can be as low as 16 Hz, which can be recorded and even reproduced, as long as the tonearm/cartridge resonance is kept substantially lower. Which is how the value of 10 Hz came to be. On this particular system, the resonance was measured at 10.5 Hz, which is close enough to our predicted value of 10.36 Hz to verify the dynamic compliance assumption.
Another noteworthy aspect of performance was the rumble, exceeding the Thorens specifications of -72 dB. The bearing and motor were reconditioned and freshly lubricated with special high performance lubricants, the capacitors were replaced, the belt was replaced with a high performance type, the clutch pulley was reconditioned, and the motor was powered by a quartz-locked power supply unit, offering a dead-stable 50 Hz, clean and pure.
Moreover, rumble measurements via tonearm and cartridge will of course give slightly different readings if a different tonearm or cartridge is used. We used the silent grooves of test records (pressed vinyl) and test lacquer disks we cut in-house for such measurements. The figure of -78 dB was obtained with the final setup, including the SME tonearm and vdH cartridge, after approximately 30 minutes of running at 45 RPM. The measurements were repeated at both speeds.
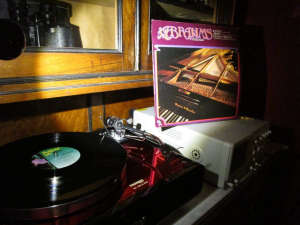
Finally, when the adjustment and calibration have been successful, the system is ready to reproduce some real music!
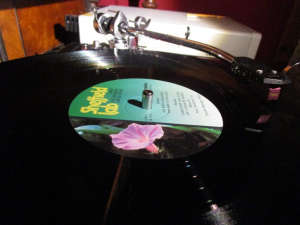
Sheffield Lab 4: Lincoln Mayorga plays Brahms, Handel, Chopin is
This is a direct-to-disk recording by Doug Sax, recorded on May 18 – 29, 1976 in Wylie Chapel of the First Presbyterian Church of Hollywood, California. The piano was a Mason and Hamlin, tuned by Keith Albright. The disc was plated by Richard "Slim" Doss at AFM Engineering and pressed at Teldec, in Germany.
A stunning recording of a beautiful performance, this record really demonstrates what the disk medium is capable of capturing, as well as what Lincoln Mayorga was capable of playing, with no technical assistance.
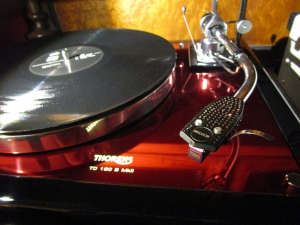
Moving on to experimental electronic music, to test how this system can cope with the strange waveforms of electronically generated sounds.
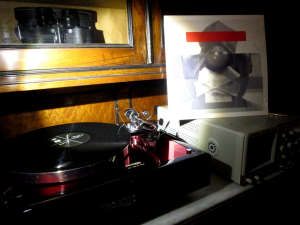
Drunk Confident – Broken Machine was recorded from 2015 to 2017 by Taren McCallan-Moore in Cambridge and Canterbury, UK. Instruments used included a Marantz CP-430, Superscope C-205, Formanta Polivoks, Moog Prodigy, Roland TR-606, Roland CR-5000, Wem Copicat and a Hsinghai upright piano. Field recordings were also made in and around Canterbury, Cambridge, London and New York, on cassette tape.
The master lacquer disks were cut by J. I. Agnew at Magnetic Fidelity. It was plated and pressed at Pallas in Germany. It's highly-recommended listening for a detailed and highly analytical insight on machine-made sounds can be successfully combined with manipulated natural sounds.
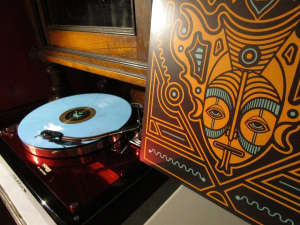
Moving on to rock music, here's a natural-sounding and dynamic recording of a band that can cover the entire range from whispering soft to screeching loud.
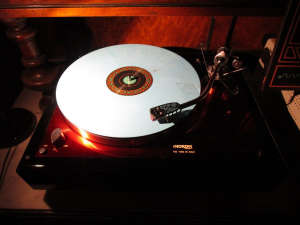
Recorded in 2017 on analog tape at Magnetic Fidelity by J. I. Agnew, it's an all-analog project from start to finish. The masters were cut directly from the 1/4" master tape at Magnetic Fidelity, and plated and pressed at Pallas.
It's a fine performance by Naxatras that proves that multitrack recording is not necessary for an excellent rock recording, and neither is any form of digital equipment. The uninhibited dynamics of the music, particularly impressive on the drums, make good use of the dynamic real estate available on the disk medium. This release is a triple-LP, keeping the sides short and sound quality high.
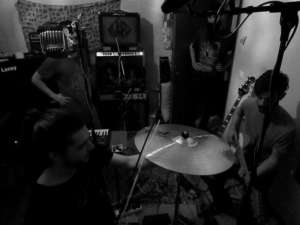
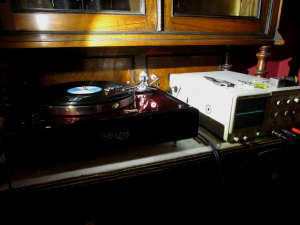
Agnew Analog Reference Instruments supplies disk recording and reproducing equipment for the recording and disk manufacturing industry, broadcasting facilities, archives, the sound restoration and preservation sector, and the discerning audiophile. They also offer engineering consulting services for equipment manufacturers, restoration and modification of high-quality phonograph record reproducing equipment, custom test records, custom precision parts, and calibration/measurement services for demanding applications. In addition, Agnew Analog offers disk recording lathes and complete disk mastering systems.
Header image courtesy of Wikimedia Commons/Hans Dinkelberg. All other images courtesy of Agnew Analog Reference Instruments.
This article originally appeared on the Agnew Analog Reference Instruments blog and is used by permission.